Automatic tool change system
When manufacturing large gears, the demands regarding surface quality of the ground tooth flanks are increasing. At the same time, ever shorter grinding and set-up times are required to increase cost efficiency. To combine maximum productivity with the highest machining quality, we have developed an automatic tool change system. This allows the use of multiple grinding tools for different grinding operations.
Increase in productivity
For most gear grinding applications, usually a grinding wheel specification is used that offers a compromise between productive roughing and high surface quality after finishing. Depending on the grinding task, the desired grinding wheel topography is set by means of dressing. An automatic tool change system enables the use of an optimized tool for roughing to remove most of the material as productively as possible. A subsequent tool change is then automatically executed to use a special finishing or fine grinding tool for the last grinding steps. In this way, the advantages of both grinding tools are combined to achieve a more productive grinding process and at the same time improve the surface quality of the finished part.
Fine grinding wheel for the highest surface qualities
By using fine grinding wheels, surface qualities of Ra < 0.2 μm can be achieved. The time required to change tools from the rough grinding wheel to the fine grinding wheel can be reduced by at least 90 % with the automatic change system compared to manual changes. When machining a typical planetary gear for wind power applications, the production time can be reduced by around 18 %.
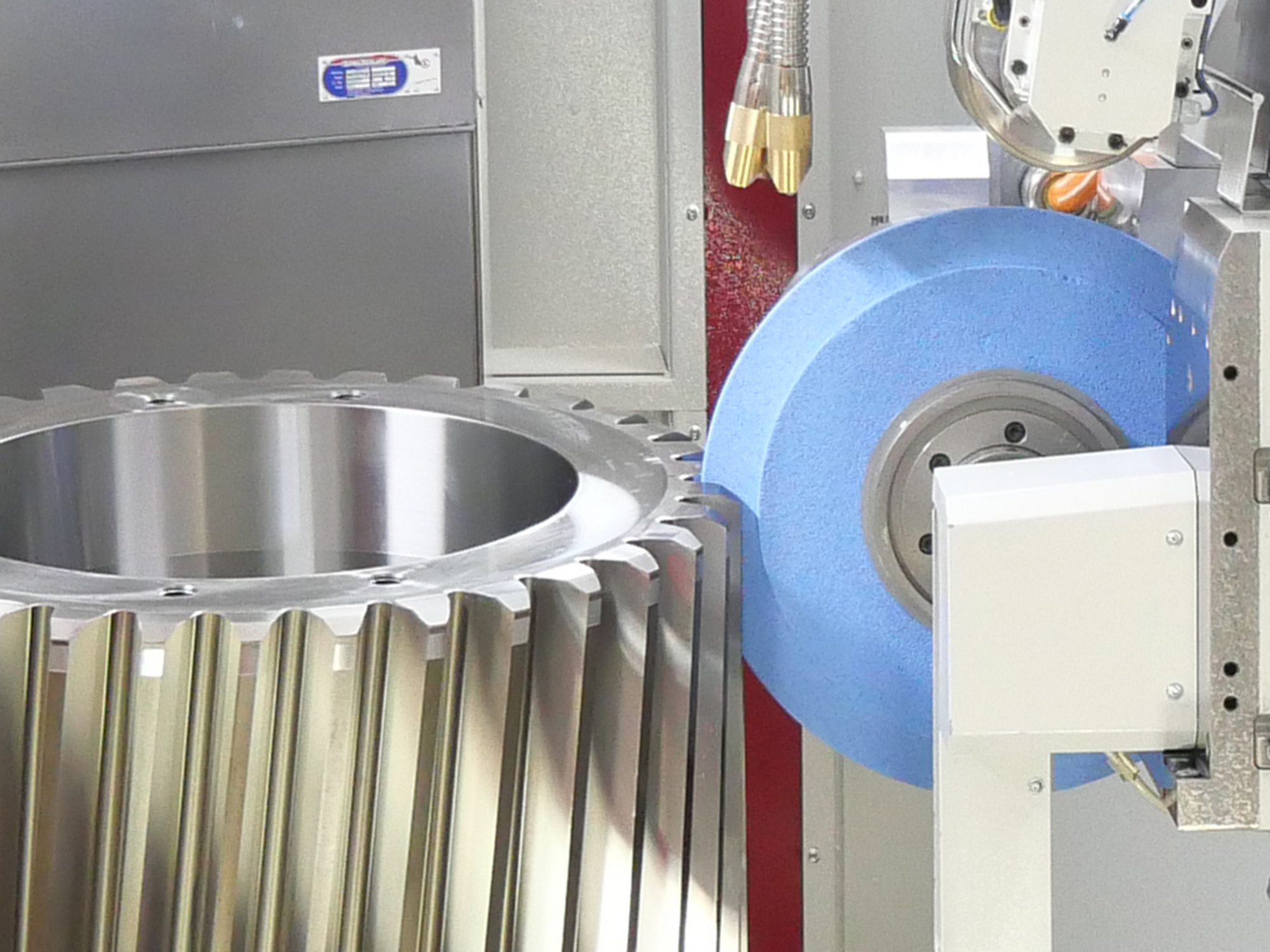
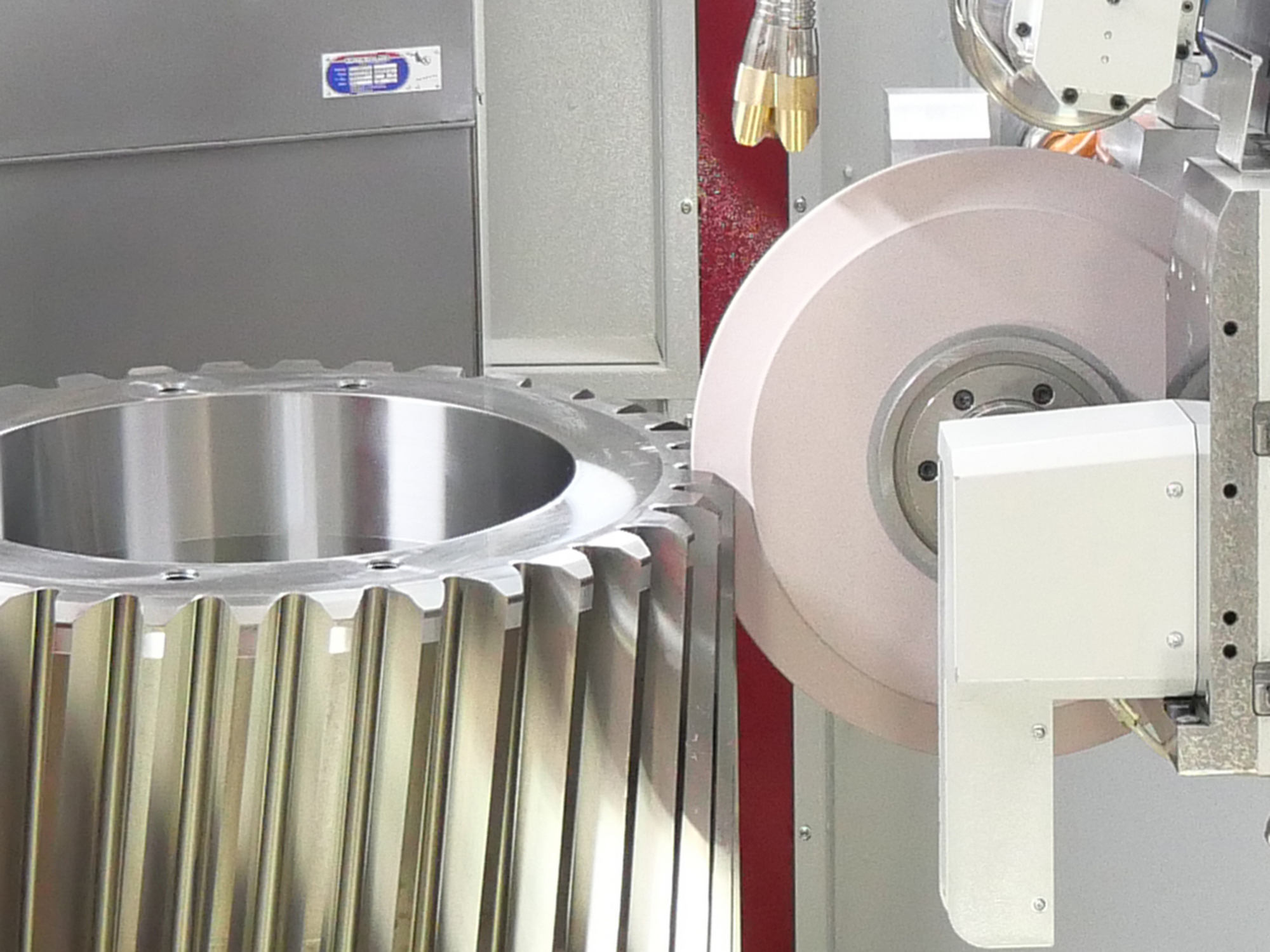
Mono grinding wheels for a high performance roughing process
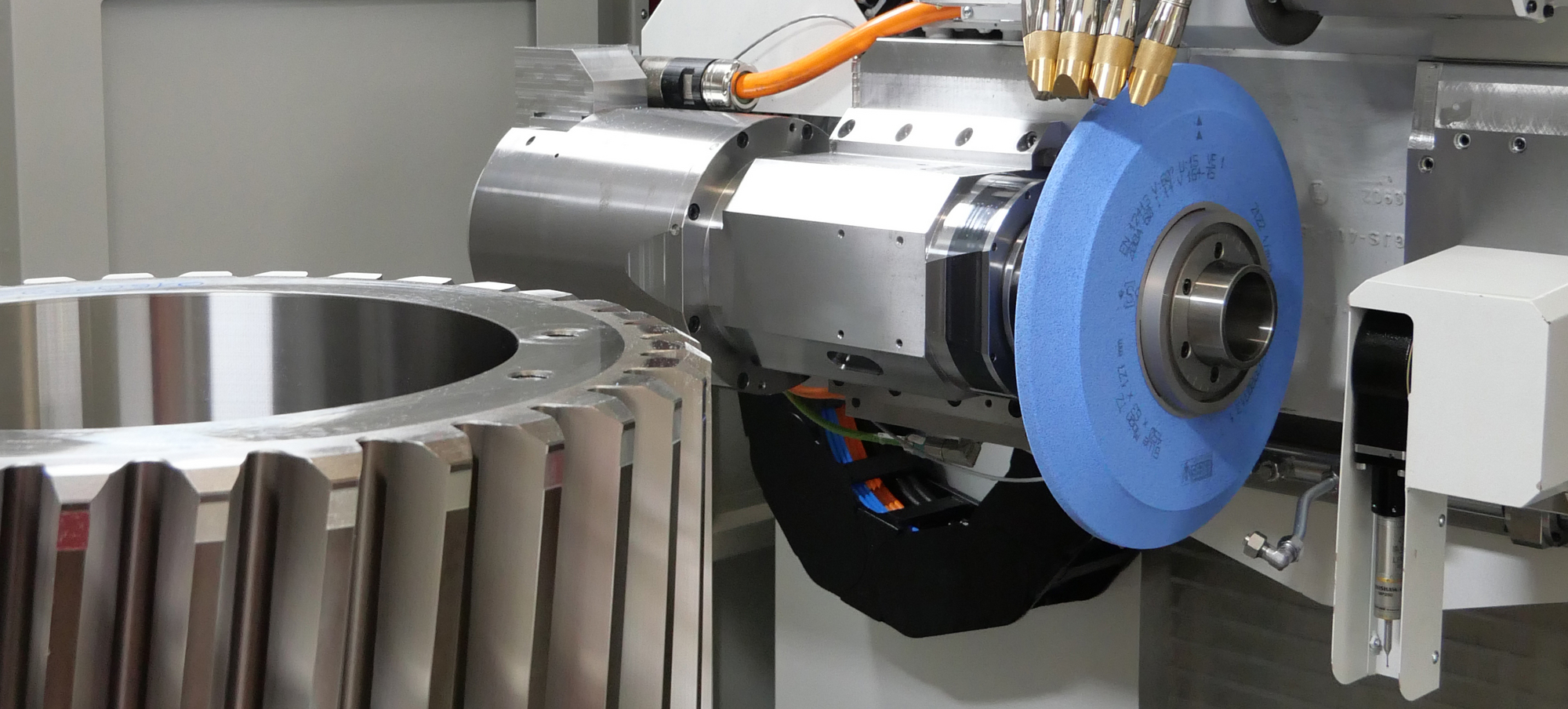
The use of an automatic tool change system can also be advantageous for standard applications. The ability to use special tools for each grinding step (mono grinding wheels) means that higher productivity can be achieved during roughing than with a compromise grinding wheel.
High-performance roughing wheels enable very high specific material removal rates Q'w. For an exemplary workpiece for the wind power industry, the grinding time has been reduced by 14 % by using specialized grinding wheels for each grinding operation.
Calculate your productivity increase
Use our productivity calculator to find out how you can benefit from KAPP NILES' automatic tool change system. A more productive grinding process brings you significant benefits, especially in serial production. You can adapt the default values in the calculator quickly and easily to represent your current production process and thus, determine your individual benefits of an automatic tool change system for your company.
An automatic tool change system is advantageous for different use cases. With the calculator, you can consider two scenarios: the use of a fine grinding wheel for the highest surface qualities and the use of mono grinding wheels for a high-performance roughing process. Immediately after entering your values, you will learn how many additional workpieces per day / per year you can manufacture using the automatic tool changinge system from KAPP NILES.
We are happy to individually check for you, how you can benefit from the automatic tool change system.
White Paper
Automatic tool change system for profile grinding of gears
Learn more about the technical background, potential applications and individual benefits for your company in the white paper by Janis Thalau, Manager Technology Development Large Gears at KAPP NILES.
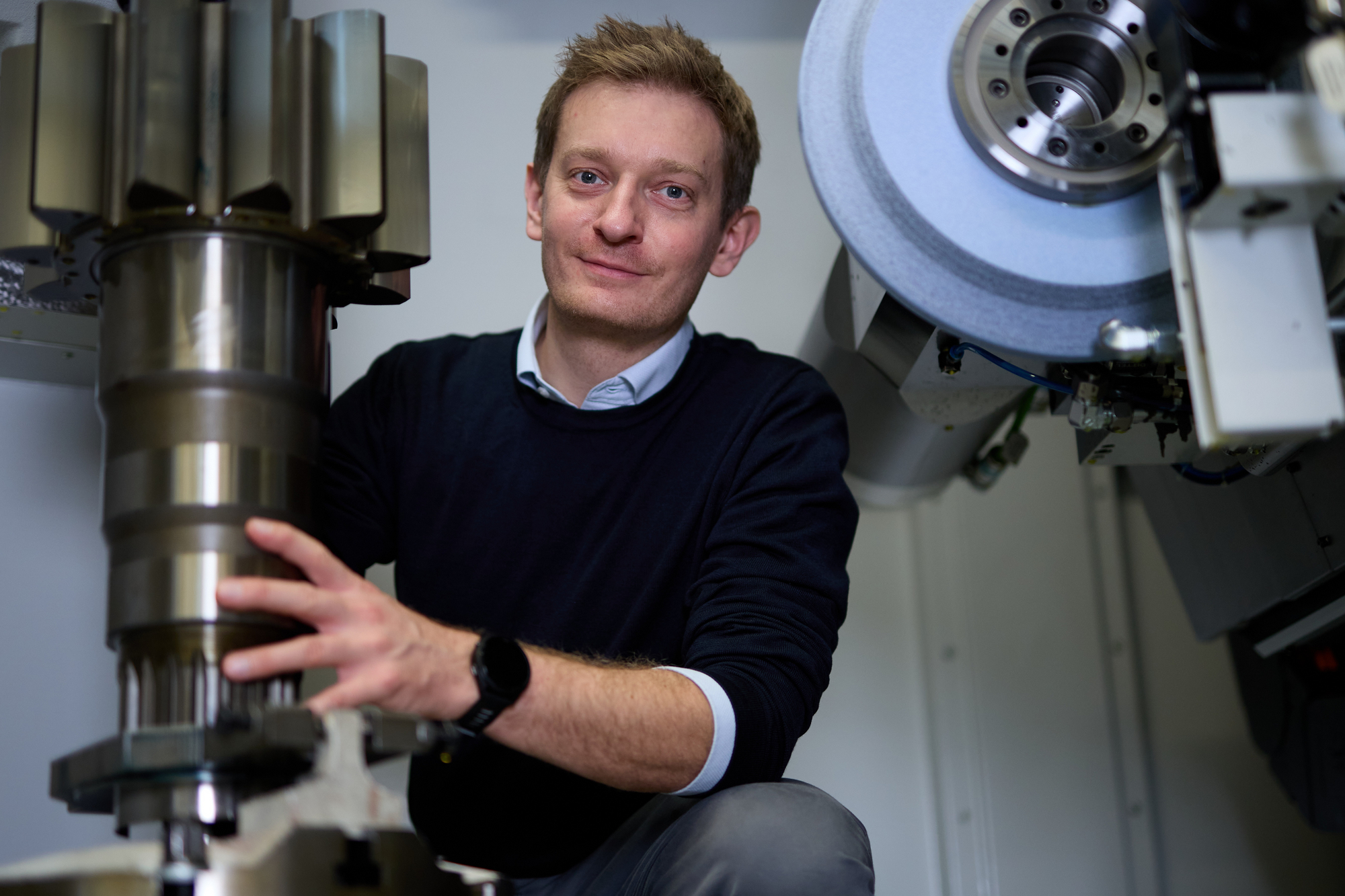
Features
- Ergonomic set-up of the tool changer parallel to primary processing time
- Complete tool change including spin cycle < 2 minutes
- Improved ergonomics thanks to set-up outside the machine
- Simple tool mounting thanks to the use of a standardized HSK interface
- Reduction of the number of dressing cycles thanks to reproducible grinding wheel positioning
- High reliability thanks to the integration of the balancing electronics and sensors directly in the spindle instead of in the exchangeable flange
Technical data
max. workpiece diameter | 3.000 mm |
max. tool diameter | 450 mm |
max. tool width | 150 mm |
max. loading weight (flange + tools) | 50 kg |
Number of tool compartments | 3 |
Tool holder interface | HSK 125 |
Tool changing time | < 2 min |
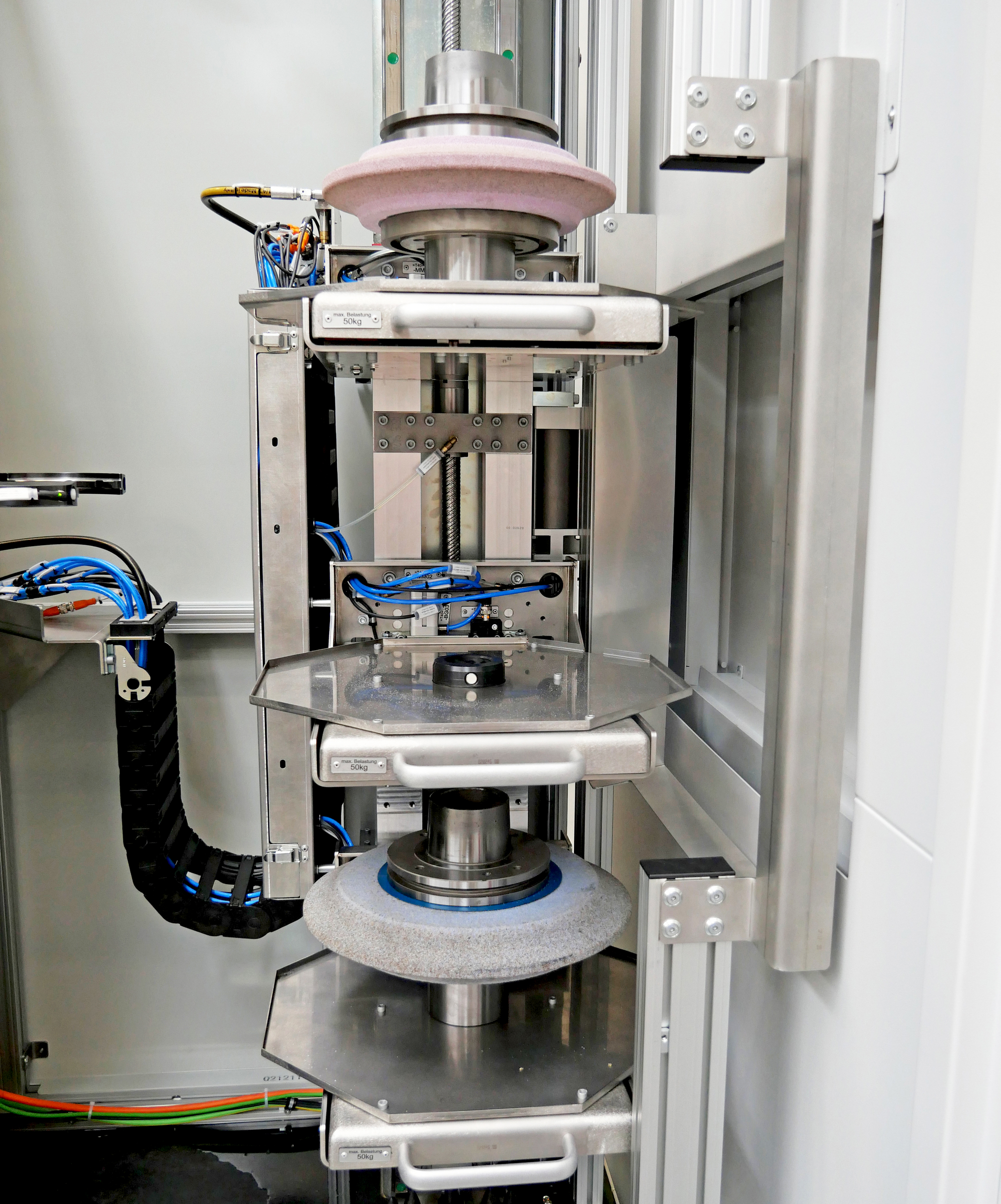
For profile grinding machines of the following series
ZP series
KNG master series
Application example: wind power
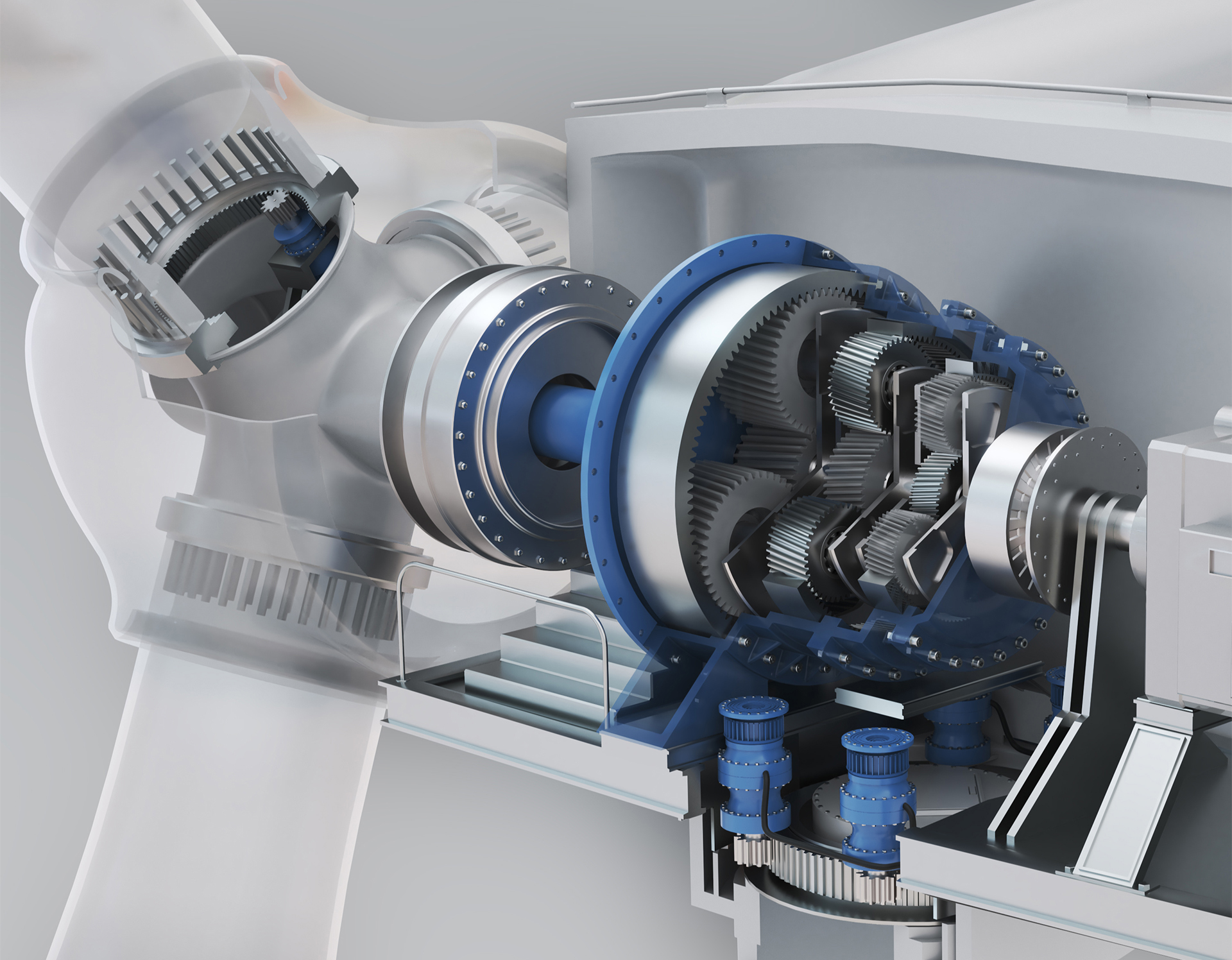
The surface quality requirements of modern wind turbine gearboxes increasingly demand fine grinding after conventional grinding. In order to produce the large number of planetary gears economically, manufacturers are increasingly using an automatic tool change system. This enables the shortest grinding times to be achieved with the highest component quality.
Contact
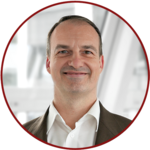
Holger Staub
Head of Sales Asia & CIS
“I will be pleased to show you how to benefit from our automatic tool change system in your production.”